New addition to Rensselaer manufacturing education environment proves to be well-timed
August 24, 2021
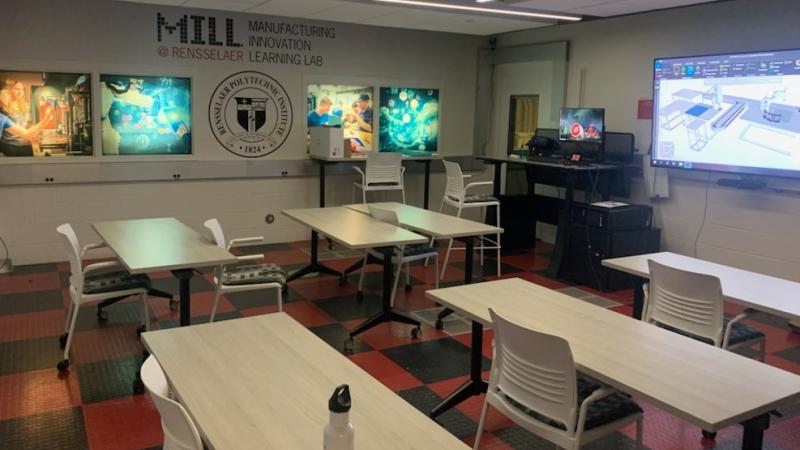
In the middle of the COVID-19 pandemic, social distancing protocols did not slow Rensselaer Polytechnic Institute students Wyatt Delans and Jake Szottfried down when they needed to design and develop code for a robotic system capable of assembling a model trophy for a class project. Using new simulation and virtual reality lab capabilities at the university, they were able to design most of the project in their dorm rooms and then test it in a virtual environment before physically manufacturing it in the Manufacturing Innovation Learning Lab (MILL) at Rensselaer.
“When you have the headset on, it’s almost identical to being in the shop,” said Szottfried, who is majoring in aeronautical engineering. “It gives you a really good sense of scale, and what needs to work and what needs to move.”
The software and hardware technology that made this virtual manufacturing possible was designed and beta tested at Rensselaer in the new Hearst Digital Manufacturing Lab (HDML) before the COVID-19 pandemic. When the Institute temporarily shifted to remote and hybrid learning, the Hearst Lab became all the more critical.
“These simulation systems allowed us to keep pace with the project tasks and kept the students on schedule,” said Sam Chiappone, the director of the MILL at Rensselaer, of which the HDML is a part. “It really was great to see how the teaching in the MILL really kept pace with how simulation and VR are being used by industry; especially given the COVID pandemic.”
The initial impetus for the Hearst Digital Manufacturing Lab’s creation was a steady shift in industry toward designing and testing new machines and manufacturing systems on virtual platforms — a migration aimed at saving time and money by testing a system out before physically building it.
The lab was made possible by a $150,000 grant from the Hearst Foundation, which enabled the purchase of simulation, and virtual and augmented reality technologies such as software, headsets, monitors, and hardware. An additional teaching and learning grant provided by Rensselaer allowed Chiappone and his team to develop simulation exercises for students that could be used with the augmented and virtual reality technology. Especially after its successful implementation earlier this year, Chiappone said that the Hearst Lab and accompanying virtual software will continue to be an essential part of the manufacturing curriculum moving forward.
“Digital and immersive manufacturing tools and simulations free our students from the constraints of a physical laboratory, allow them to experiment with their ideas in a safe environment, and then put those ideas to work in the MILL,” said Shekhar Garde, dean of the School of Engineering at Rensselaer. “The Hearst Lab is helping us bridge the gap between the cyber and the physical, which will become increasingly important for careers in the post-COVID world.”
Delans and Szottfried recognize that this experience gives them necessary skills.
“The software that we learned is not some random program; it’s the standard for a lot of things,” said Delans, who graduated in May with a degree in mechanical engineering. “I feel that prepares us and gives us an edge.”