February 14, 2024
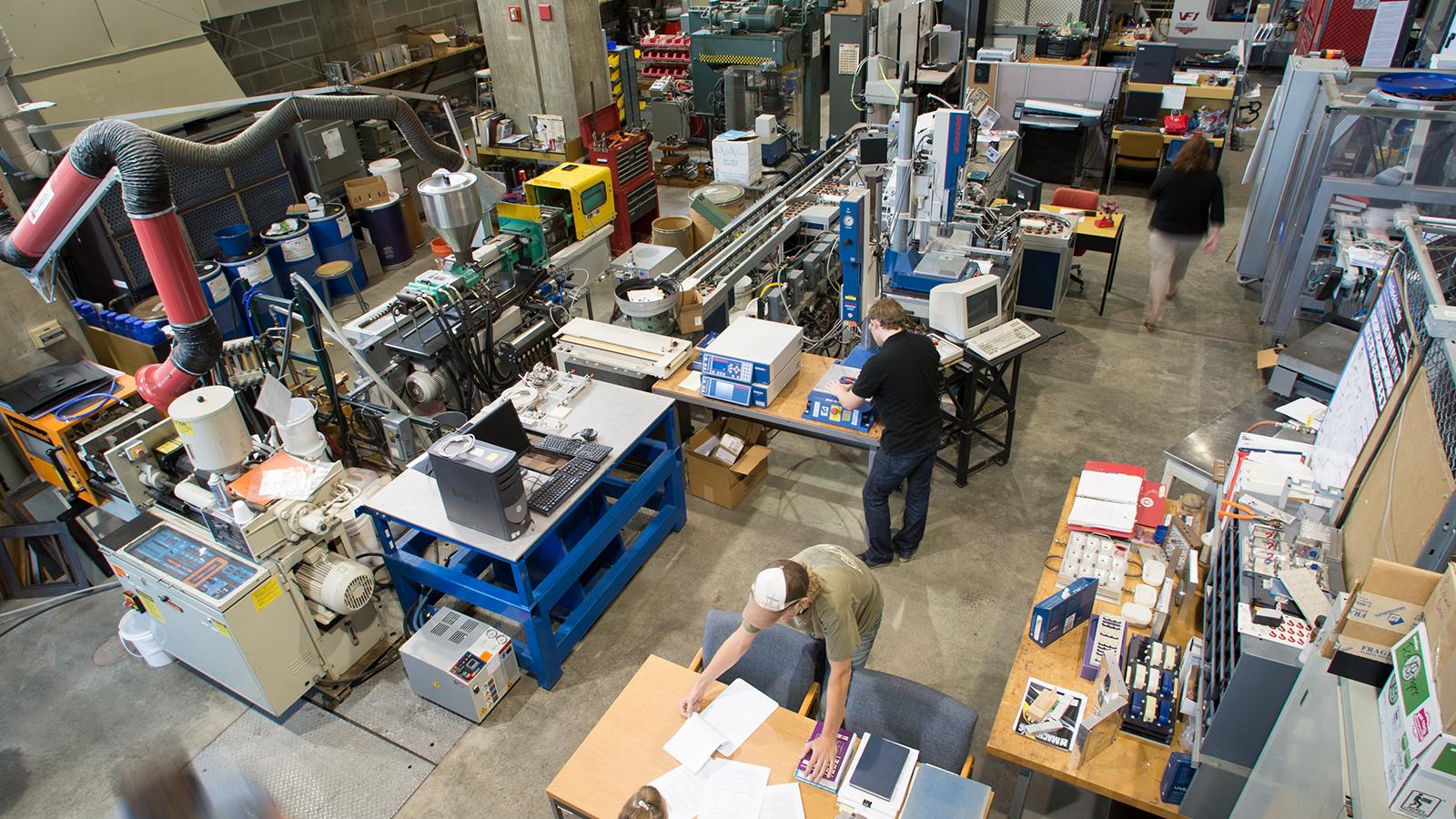
From computer chips and pharmaceuticals to batteries and airplanes, our world runs on manufactured goods and products. However, most people rarely think about how these things get made — not to mention the technology and engineering that goes into making them at scale.
For more than four decades, students in Rensselaer Polytechnic Institute’s Manufacturing Innovation Learning Laboratory, or MILL, have spent whole semesters learning just that, gaining hands-on experience taking an idea and turning it into a finished product.
Today, those skills are more important than ever, said Shekhar Garde, Ph.D., dean of RPI’s School of Engineering.
“Advanced manufacturing is not only needed to take scientific and technological innovations from the lab to the market, but it is also at the heart of onshoring manufacturing of high-value products in the U.S.,” Garde said. “Graduates of the MILL go on to successful careers as leaders in top companies as well as independent entrepreneurs.”
In step with the times, the MILL, originally called the Advanced Manufacturing Lab, or AML, has transformed over the years.
“From the original 400-square-foot room to the 3,000-square-foot space we have now, our facility has grown by leaps and bounds in its 40 years,” said Sam Chiappone, director of manufacturing innovation in RPI’s School of Engineering. “The technologies, industrial support, curriculum offerings, and resources available to our students are more robust today. I have a six-inch binder on our 3,000 alumni, who are now working in firms such as Sikorsky, Regeneron, BD, Boeing, GM, Tesla, SpaceX, GE, Apple, and many local manufacturing companies. Alumni have also started companies of their own.”
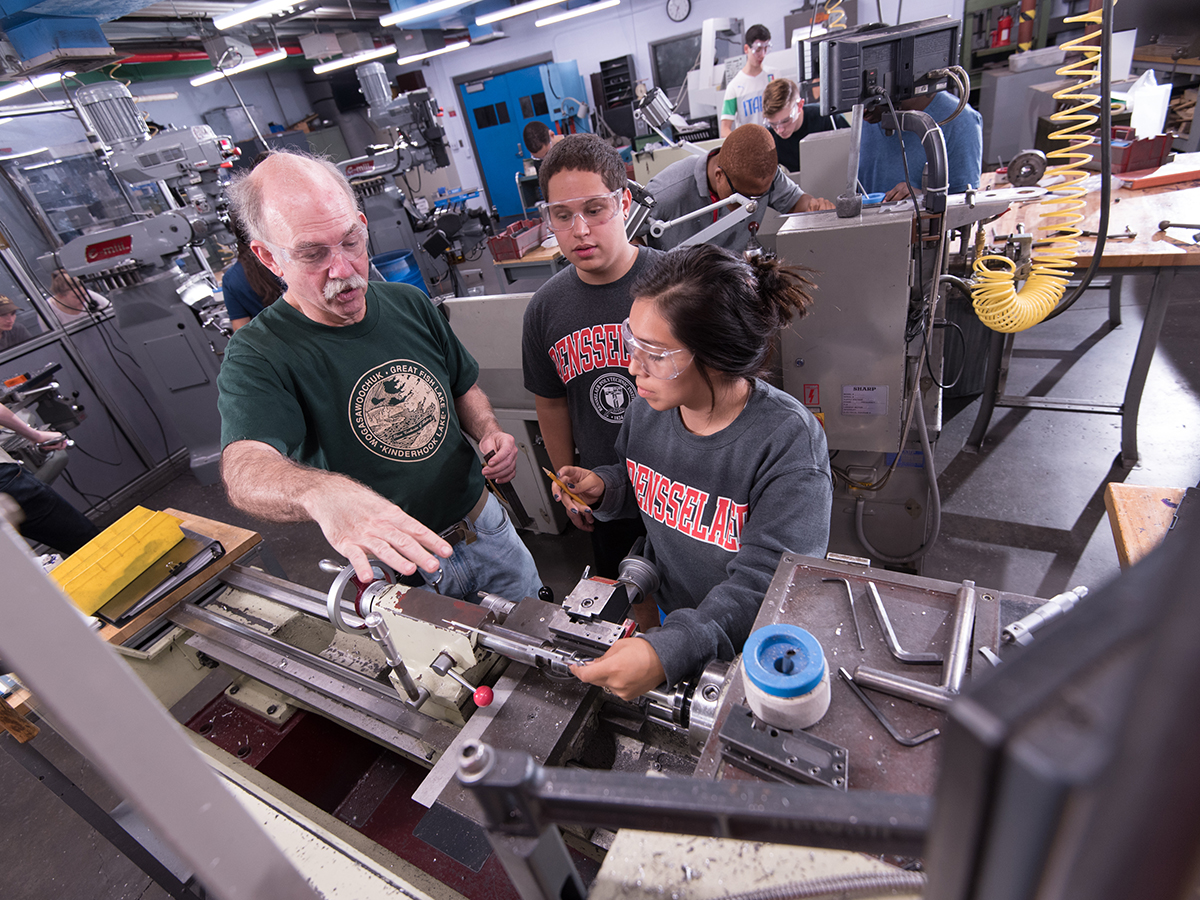
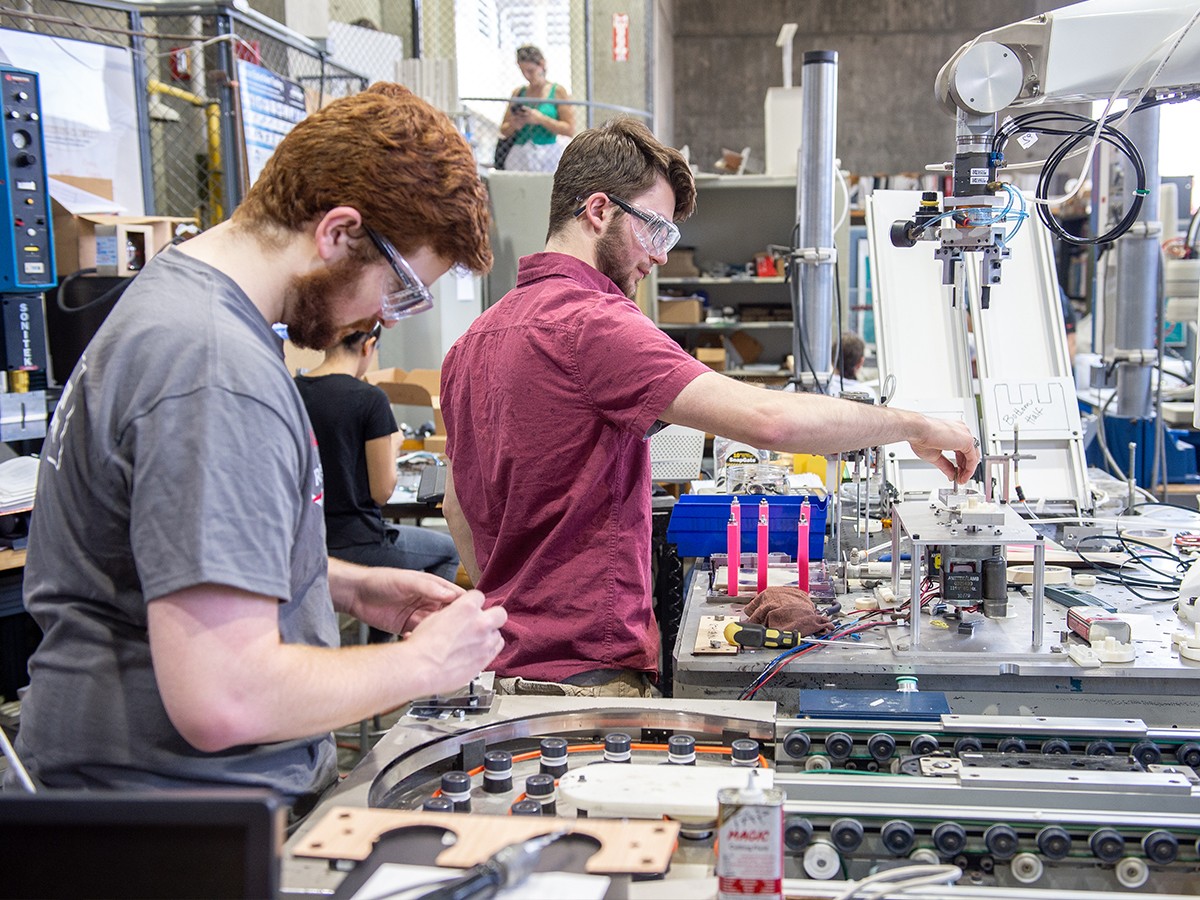
Manufacturing Processes and Systems, or MPS, which Chiappone teaches, is the MILL’s capstone course. Using the MILL’s computer-controlled machine tools, lasers, robots, 3D printers, injection molders, ultrasonic welders, and more, students design, prototype, and manufacture a unique product over the course of a semester. Students in the class also learn from industry experts serving as sponsors of the MILL, offering them elite training opportunities to work in modern manufacturing companies.
MPS students, class alumni, faculty, and staff are regularly recognized through the American Society of Mechanical Engineers (ASME) Student Manufacturing Design Competition and the Society of Manufacturing Engineers (SME) Annual Conference Student Competition.
“The MPS lessons teach students how to transform computer-aided design concepts into reality. Students apply lessons in tolerances, shrinkage from molding, and design for robotic assembly. In other words: real life!” said Stephen Derby ’76, ’77, ’81 Ph.D., professor emeritus and faculty member of the AML. “Applying engineering to a real-life manufacturing lab was the original intent of AML 40 years ago, and it still is true today. That is what is unique about the MILL.”
MILL’s industrial sponsors help to ensure the curriculum focuses on current and future best practices and evaluate student performance from a professional perspective. Over the years, industrial sponsors have assisted in updating the curriculum to include lessons in manufacturing and assembly simulation, smart manufacturing, digital work instructions, and advanced machine tools including 5-axis milling. Currently, industry experts Larry Oligny Sr. ’16, ’20 M.S., engineer, and Maddie Dwyer ’19, ’20 M.S., academic engineer, are supporting students in the MILL.
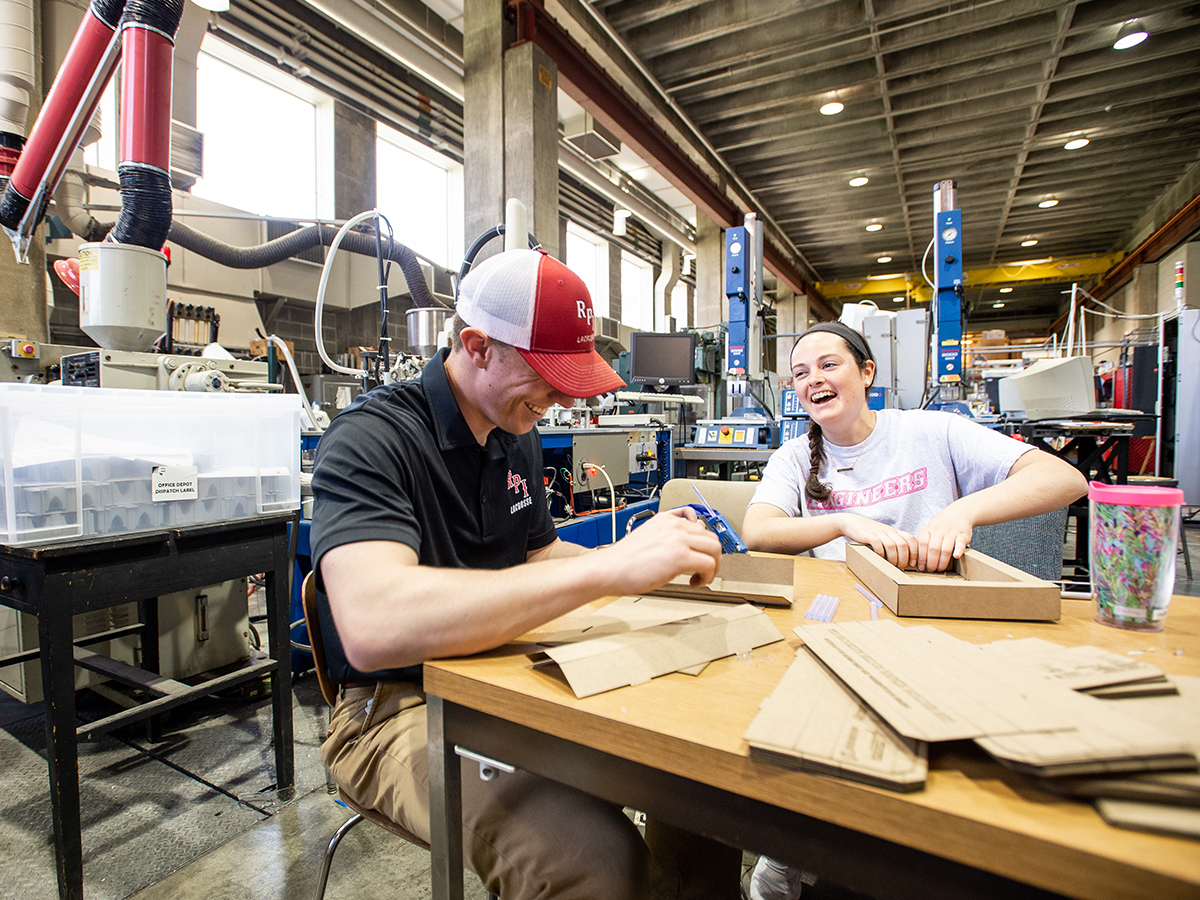
Ammar Barbee ’24 is president of RPI’s Society of Manufacturing Engineers (SME). “The academic program in manufacturing at RPI is unique,” he said. “Inspired by the concept of a teaching hospital, the MILL is our teaching factory. I feel lucky to have benefited from training at the MILL, learning from RPI’s and industry experts, and even being able to take part in advanced manufacturing research as an undergraduate. So many professional opportunities will be available to me as a result.”
“In 1987, I had the privilege of taking the AML class at RPI. This experience served as a pivotal cornerstone in the foundation of my career in aerospace manufacturing,” said Stephen E. Lindsey ’88, chief technology officer of Hanwha Aerospace USA. “The hands-on experience and skills that I gained played a vital role in kickstarting my journey into the jet engine manufacturing world. I am proud to join in celebrating the RPI MILL’s 40-year legacy of excellence in shaping the careers of manufacturing professionals like me.”
The MILL’s current industrial sponsors include:
Allendale Machinery – Haas Factory Outlet
Becton Dickinson (BD)
Boeing
DAPR Engineering
Hanwha AerospaceUSA
LoDolce Machine Co. Inc.
Lutron
Mainstream Engineering
Mastercam
NSH USA Corporation
Putnam Precision
RBC Bearings Inc.
Sandvik
Sikorsky
Snap-on
Specialty Silicone Products (SSP)
Universal Robot (UR)
Visual Knowledge Share Ltd. (VKS)